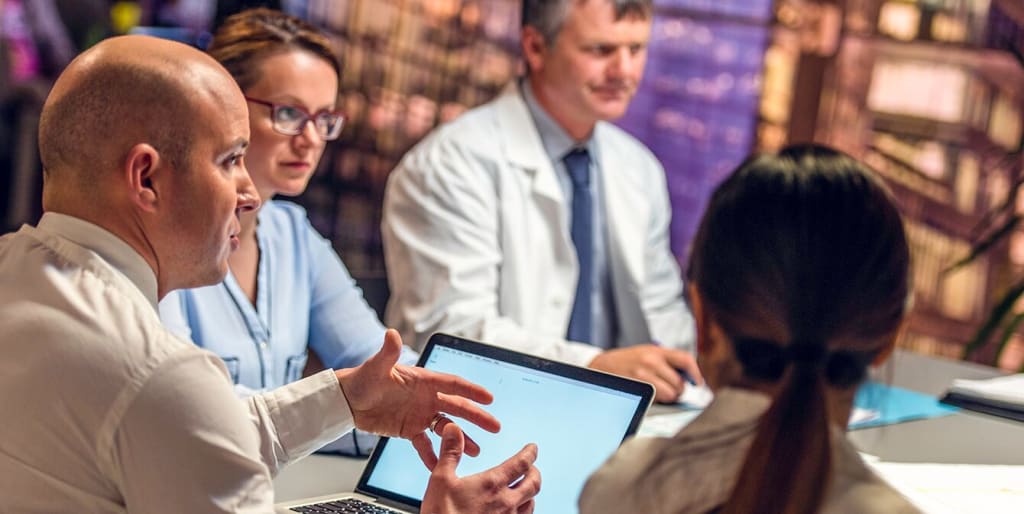
Why understanding asset failure produces better outcomes for healthcare facilities
Reliability-centered maintenance (RCM) identifies asset failure. When your equipment or assets fail, operations grind to a halt. When life-saving equipment fails, there’s much more at stake. What happens when the lights go out in an operating room or power goes out on life-support equipment?
RCM identifies asset failure before it becomes a reality. Developed in the 1970s by the aviation industry, where failures are catastrophic, RCM principles were later adapted to other sectors, including healthcare.
In a recent webinar hosted by the American Society for Healthcare Engineering (ASHE) in partnership with JLL Technologies (JLLT), a panel of experts shared their expertise and insights about RCM and how valuable it is to the healthcare industry.
RCM is proactive
Russ Parrish, JLLT vice president of account adoption and optimization, shared how RCM is a proactive process. It allows facilities management (FM) teams to anticipate failure points, assess risk, and design responses to mitigate impact. In healthcare applications, RCM focuses on essential medical equipment and processes. It incorporates preventive maintenance, data, and technology—such as information from your computerized maintenance management system (CMMS)—to delay or avoid failure and extend the useful life of assets.
Instead of reactive work orders, which take three times longer to complete and cost four to 10 times more than preventive maintenance, RCM is proactive. It enables you to perform the right work at the right time and reduce risks for your organization.
Benefits of an RCM program include:
• Time- and cost-savings
• Improved asset performance and longer useful life
• Real-time data, managed by a CMMS, for analysis and insights
• Increased equipment safety and decreased environmental impact
RCM in real-world healthcare situations
Hospitals need backup generators to run essential equipment during power outages. If a generator fails, people could die. While federal regulations require regular testing of emergency backup generators, these tests are expensive. Evaluating testing costs is key to both RCM and the related field of alternative equipment maintenance (AEM).
Parrish shared a story about an AEM analysis that ultimately saved a hospital $18,000 in fuel costs by moving from a weekly to monthly generator-testing schedule. Less frequent testing also prevented wear and tear on the generators and extended their useful lives.
Data is key to the success of RCM and AEM, because it enables informed decision-making. ASHE conducted a three-year study of the weekly testing of ground fault circuit interrupter (GFCI) electrical outlets in hospitals. GFCIs are essential safety features in locations where electrical appliances or equipment might come into contact with water, such as in bathrooms, kitchens, and labs.
The ASHE study revealed only a 2% failure rate—an acceptable level of risk—for GFCI outlets that are tested weekly. Switching to a monthly schedule would save a projected $78,000.
Take advantage of your CMMS
Per Kevin Eaton, director of healthcare at JLLT, data is the foundation for RCM and AEM programs. You need accurate, up-to-date, and standardized data across your CMMS platform.
Maintenance results and processes—even data from IoT sensors—can be entered directly into your CMMS. Sensor data will let you know when equipment is failing, so you can respond quickly to mitigate adverse outcomes.
The data in your CMMS serves as an audit trail for assessing progress as you move from reactive to proactive maintenance. It’s also a source of actionable insights for increasing asset and equipment reliability through continual improvement.
Next steps
Discover how to start and manage RCM and AEM programs in your healthcare setting and capture the time- and cost-savings that come with extended asset lives and reduced equipment failures. Check out the recording of our recent webinar, “Reliability-Centered Maintenance: Getting Started with Technology.”